So if existing materials like haematite aren’t good enough to be used to generate solar fuels, how do researchers go about identifying novel materials to convert sunlight into fuel? We’ll see how computers can help identify ideal materials for the production of solar fuels. What are the key steps to do in research lab to build a tangible device that can be used to produce a solar fuel?
By Dr Miriam Regue and Dr Minsu Park, Research Associates in the Department of Chemical Engineering.
Oxide perovskites are a class of light absorbing materials that are gaining significant interest in the field of solar fuels. Examples are lanthanum ferrite (LaFeO3), praseodymium ferrite (PrFeO3) or gadolinium ferrite (GdFeO3). They are made of abundant elements and offer good visible light absorption. But understanding how to use them for solar fuels production is still unclear.
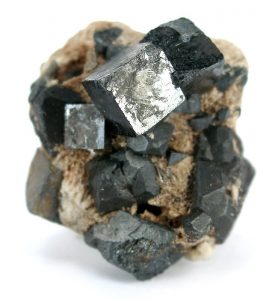
Computer modelling to identifying novel materials
The Computational Materials Science group uses computational modelling to predict the absorption properties of materials that haven’t been made yet. These calculations can also help researchers understand the how these new materials might behave before building a test solar fuel device. This is an excellent starting point to evaluate their suitability as candidates for solar fuels devices.
Computer modelling results can predict things like: how thick the material needs to be for boosting light absorption, how chemical modifications can affect the performance of a material, or how different structures of the same material can alter the optoelectronic properties.
Practical tests for confirming a good solar fuel material
Once the theoretical knowledge is gathered, the race to design an efficient device begins. From a practical point of view, the successful material candidate must be stable in water conditions for at least 2,000 hours. It must also be able to convert a minimum of 10% of received solar light into energy.
The first stage of the experimental design is to test the light absorber material at a lab scale. There are two main ways to do this:
- Depositing the light absorber material on top of a flat conductive surface to form a photoelectrode. This photoelectrode generates electric current when exposed to solar light. This current produces the solar fuel. This approach is called the photoelectrochemical method. The size of the electric current generated shows the quality of the material. Greater current, more energy conversion, better solar material.
- Directly immersing the powdered light absorber material in a reactor illuminated with solar light. This approach is called the photocatalytic method. The quantity of solar fuel gases (H2, O2, CO, CH4 …) produced shows the quality of the material. Greater gas production, more energy conversion, better solar material.
Schematic diagram of the different materials and approaches employed in the Eslava Group: Applied Energy Materials group.
Although both approaches are feasible for identifying novel materials, researchers typically prefer the photoelectrochemical approach for safety reasons, and also due to better reproducibility of the results.
Further challenges to identifying novel materials
That’s just the beginning of the practical steps to develop a material that will work well in the real world. Researchers are looking for ways to increase the efficiency and improve the performance of a novel material. They work out ways to make materials which selectively make one fuel gas product. Or materials which are easy to make reliably in large batches.
In our research group, we follow various novel approaches to improve the response of these materials and to understand and describe their behaviour. Here are some of our recent discoveries for how to improve performance of the water splitting process:
- mimicking the shape of natural desert roses on TiO2,
- using a polymer as a template for the preparation of LaFeO3 and Fe2O3
- loading copper and graphene oxide on novel halide perovskite materials.
Technology readiness level
So, what technology readiness level does solar fuel production have right now? Will we ever power our home using a stand-alone H2 device? Is our society ready to produce commodity chemicals (plastic, fertilizers, clothes…) from waste CO2 using solar light?
Right now, photoelectrochemical approaches are still in lab-scale studies. However tremendous improvement has been achieved since their discovery in 1972 by Fujishima and Honda. Researchers have achieved solar-conversion efficiencies of 10% for about 40 hours. Similar or even higher efficiencies are likely by 2025 on square metre devices. The final goal is to achieve decentralised and local production of hydrogen at a household level in the near future.
Direct CO2 capture and solar conversion is on a similar technological readiness as H2 production. However, the success of this technology relies on the capability of coupling direct CO2 capture technologies with photoelectrochemical set-ups.
Cost is king
These disruptive technologies will only be deployed at scale when they can compete economically with fossil fuel methods of hydrogen and carbon-based products production. Only then will they take market share. Currently, steam methane reforming produces H2 at an average cost of ~1.40$/kg (depending on natural gas price). This is significantly lower than a 2018 estimate for photoelectrochemical devices of 9–11$/kg. If current technical barriers are overcome, this could reach 2–4$/kg. This breakthrough will pave the way for solar hydrogen in the world’s future energy mix.
Read the first two blogs in this series: why solar fuels are needed, and what properties are needed by solar materials.