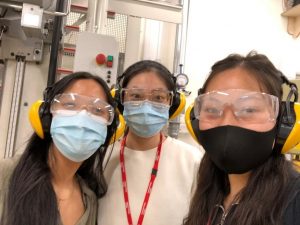
Undergraduate students, Jiayue Feng and Sandeepa Tuladhar (both Chemistry with Molecular Physics) and Shannan Huang (Chemical Engineering) teamed up in the DigiFAB Hackathon to build a low-cost automated liquid handling platform. Here they tell us more about the challenge, their solution and why it was such a valuable experience.
By Jiayue Feng, Shannan Huang and Sandeepa Tuladhar
Learning more about the tools of our trade
Digital chemistry can potentially revolutionise the industry due to the rate at which discoveries can be made. An automated pipetting system can be accessed in the Molecular Sciences Research Hub (MSRH) but is not suited for all types of chemicals and large volumes of liquids. Digitalising reduces the need for manual labour and time, but still maintains high precision. Therefore, such an automated platform can save scientists from tedious and repetitive benchwork to focus more on designing experiments and analysing data.
Studying chemistry and chemical engineering we often rely on using instruments such as liquid handling platforms, yet we focus little on the mechanism of the instrument itself. Through this project we hoped to gain insights into how the equipment we use works, its drawbacks and how such machines can be optimised and improved.
Our challenge and how we hacked it
The challenge was to build and programme an automated robotic platform to handle/transport multiple vials of liquids, whilst most importantly, being accessible and low-cost. Most commercially available liquid handling platforms cost well over hundreds of thousands of pounds, meaning barriers to access to these machines are a significant issue. We aimed to build a prototype which could automate many types of chemical reactions, handle a variety of harsh chemicals, be programmable with Python and consist of a reproducible and easy-to-assemble build.
We approached this challenge using a modular method by creating a timeline and focusing on one section at a time. Although we only made one prototype, many prototypes of the individual parts were made. First, we mind-mapped potential materials, given that the platform would need to handle a range of pHs as well as chlorinated and non-chlorinated solvents. We resolved to use PTFE, borosilicate glass and stainless steel for any components that would come into contact with the solutions.
To design, 3D print, and laser cut multiple components we used Autodesk Fusion 360 software. After a couple of iterations, the current version of the needle holder was printed (we named it Darth). Adapters were also designed and printed to connect and x- and y-axes linear rails to the linear bearings, allowing movement across the span of the frame.
Simultaneously, we attempted to code the motors and syringe pump. To control the motor using Raspberry Pi, we consulted many websites such as GitHub. After understanding the basics, we learned from other’s work and created our own Python code. A challenge arose when we realised that there was no suitable cable to connect the serial port of the pump to the Raspberry Pi. Instead, we made a compromise cable of three wires that were used for the main commands: start/stop, direction, and ground, which was sufficient to push and pull the syringe.
In the last two weeks, we designed a vial rack and cut it from a thick acetal sheet with the aid of the DigiFAB team and the Hackspace staff (especially David Miller!) All the components, including the syringe pump, the motors, the needle component, a three-way valve, a holding loop, and belts that were fixed by tooth pulleys, were assembled and finetuned. Finally, the codes for each stepper motor, the syringe pump and the wash pump were combined.
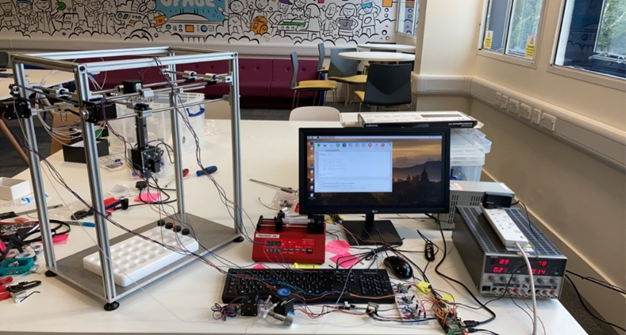
Hack help with the hardware and software
During the project, a great deal of support was provided by the Hackspace crew: from debugging our codes to teaching us how to use the tools available, such as the laser cutters and 3D printers. They were also very friendly and always willing to help, creating a safe environment for us to feel comfortable to ask for help and make mistakes.
Our team gained a great deal of knowledge in programming the various components in Python and learning about basic electronics. We also rapidly learned how to use a new piece of software, Autodesk Fusion 360, which was necessary at each stage to design components to be 3D printed and laser cut.
On the hardware side, we all gained valuable practical experience in using new tools and equipment. We learnt how to use Ultimaker Cura 3D printers, including knowledge of nuances such as optimal orientation. We also learnt how to set up a laser cutter for different materials, how to bend acrylic to certain angles, and how factors such as frequency, speed and power should be altered depending on the material when laser cutting. Our team gained experience in soldering a variety of components and assembling many different fittings, as well knowledge of small details like the two different types of screws and screwdrivers to match.
The fourth floor
Towards the end of project, we had the opportunity to visit the fourth floor of the MSRH. It was an insightful experience to be able to see the Opentrons automated liquid handling platform in action, and to hear from researchers about the issues of the existing robot and the attempts made to troubleshoot. It was also interesting to compare it with our prototype and realise how its features helped to resolve some issues with the existing automated platform.
Teamwork tips
One of the most useful tips for generating inspiration would be mind-mapping. Working as a team, we first generated many ideas to the problem, no matter how “off the wall” they seemed to be. Then, through discussion, we reviewed those ideas and selected the best one that suited the existing design.
An unforgettable experience
Overall, this has been an unforgettable learning experience for us and an incredible way to spend the summer. Some of the most memorable moments include making our first prototype of Darth, using the angle grinder, struggling to troubleshoot the issue of the ghost motors for ages, Jenny’s DAILY Paul ham sandwiches and learning how to say Eifion’s name!
Find out more
- Find out what the other 2021 DigiFAB Hackathon team got up to!
- The Institute for Digital Molecular Design and Fabrication – DigiFAB
- Postgraduate studies in Digital Chemistry
- Imperial Advanced Hackspace
Thank you
A huge thank you to the DigiFAB leads (Dr Becky Greenaway and Professor Klaus Hellgardt), their graduate students (Annabel Basford, Benjamin Egleston, Ciaran O’Brien) and the Hackspace team (especially David Miller) for their support in making this hackathon happen, and many thanks also to DigiFAB for organising, and DigiFAB and the Department of Chemistry for funding.