Professor Baptiste Gault is a Professor of Materials in the Department of Materials and leader of Atom Probe Tomography research at the Max-Planck-Institut für Eisenforschung. He is the Group Leader for Atom Probe Tomography.
Atom Probe Tomography is the only material analysis technique offering extensive capabilities for both 3D imaging and chemical composition measurements at the atomic scale. Since its early developments, Atom Probe Tomography has contributed to major advances in materials science.
In this blog post, Professor Baptiste Gault shares more about Atom Probe Tomography, his research journey and how materials will be crucial in transitioning to a zero-carbon world.
Can you tell us more about Atom Probe Tomography?
Atom probe tomography is a growing microscopy and microanalysis technique that provides three-dimensional compositional mapping with sub-nanometre resolution and a sensitivity that goes down in the range of parts-per-million across all elements of the periodic table. This essentially means that we can take a small piece of material and measure very locally and with a high precision how much there is of each element inside and how they are distributed with respect to one another.
Why is this interesting, you might ask…? In any given material, the way the atoms of the various components are organised controls the properties of interest of the material. If we wish to design materials that are stronger, more active, more resilient against failure, then we need to understand what in the atomic structure and distribution underpins these properties and how these evolve during service. That’s where atom probe tomography becomes useful: it can complement existing techniques – think optical and electron microscopies, wet chemistry or X-ray based diffraction and spectroscopies, for instance – and provide compositional analysis on an unparalleled scale. The facility that we’re establishing at Imperial will enable us to deploy multiple microscopy techniques on the same specimen to obtain structure and composition from correlating electron-based techniques and atom probe tomography.
The field has been expanding and evolving really fast in the past decade. During my PhD studies, there were more than a dozen groups worldwide and maybe 20 instruments in operation. Today there are over 120 and the community is growing. We described these recent developments and how the atom probe works in this Nature Reviews Methods Primer article published in late July.
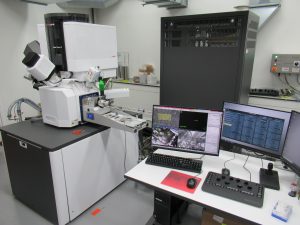
What led you to research this area of Materials Science?
That’s a tougher question than you might think… like many other things in life, they often happen. I studied both physics and chemistry as I intended to become a secondary school teacher, then ended up picking up a master degree and materials science seemed closer to my interests; the list of internships had one with a recently appointed lecturer who seemed nice and fun, and I got into atom probe then… this might have been a trap!
I was then awarded a scholarship for a PhD and decided to continue working on the development of the atom probe instrumentation during my postdoctoral work and then as a senior scientist and now academic. I’ve kept an interest in method development and in the application of the technique to an ever-increasing range of materials systems and problems. It’s good fun, and I keep learning from all the amazing folks I end up collaborating with – that’s the most interesting side of this entire endeavour.
What are the main aims of your current research?
So my research really had two main directions.
On the one hand, “push the analytical limits of atom probe tomography” – this was my mission statement when I started my first postdoc at the University of Sydney in 2007 and still applies today. So part of the work of my close collaborators is a consequence of the development of new instrumental protocols, for instance, how can we transport samples from one instrument used for the preparation of suitable specimen into an atom probe while keeping them very cold (cryogenic temperature close to -200˚C) and under very high vacuum (somewhere in the range of what we find in outer space). We also work on developing methods to extract more meaningful information from the three-dimensional point cloud that we generate or to improve the reliability of the processing of the raw data from the instrument. For this, we explore the use of machine learning approaches, for instance.
On the other hand, we make use of the technique to provide insights into a range of materials, which includes steels for cars, nickel and titanium and aluminium alloys for various parts in planes, thermoelectrics and photovoltaics for energy conversion from heat or sunlight, hard and soft magnets for electric car engines or wind-power generators amongst other things. Because the microstructure of these materials is typically hierarchical and complex on multiple scales, we use a range of microscopy and microanalysis techniques which culminate with atom probe tomography performed on the bits of the material that have been identified as the most critical: the cherry on the cake.
Can you explain some of your recent results?
Materials will be critical to most aspects of the zero-carbon transition. Whether we want to extend the lifetime of engineering parts to limit the use of resources and their making, which is an important source of emissions, or design new materials with enhanced properties or activity towards enabling the hydrogen economy, atom probe can be used in complement to an arsenal of techniques to bring insights that are critical to understanding fundamental processes and apply those to engineer better materials.
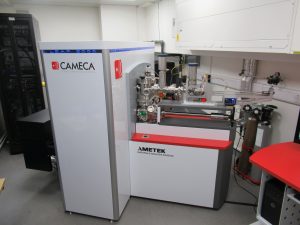
Since the award of an ERC-Consolidator grant in 2018, the group has a specific focus on the analysis of hydrogen in materials and materials relevant to the hydrogen economy. We hear a lot more about hydrogen in the media at the moment, as it is an interesting candidate for decarbonisation of aspects of our society – maybe some parts of transportation and industrial processes, including steelmaking.
Hydrogen is also known to cause or facilitate embrittlement of most metallic materials, which becomes especially critical for high-strength alloys that are necessary for making lighter cars and planes to reduce carbon emissions, for instance. Hydrogen is the lightest of elements, and it remains elusive to most microscopy and techniques, so many questions regarding its interaction with the microstructure remain open.
In the group, we make use of our dedicated infrastructure involving an atom probe and a cryogenically-enabled focused-ion beam and the possibility to transfer samples from one instrument to another. This platform, located at MPIE in Germany, served as a template for the facility that is being installed at Imperial as we speak. First, we showed the possibility and critical importance of cryogenic specimen preparation. Then, we used isotopic-labelling, i.e. introduced “heavy hydrogen” inside a material, froze the sample to prevent hydrogen diffusion out of the material and then performed analysis to map the distribution of deuterium and help narrow down on some of the hydrogen embrittlement mechanisms and mechanisms of hydride growth. We use this knowledge to design new alloys as well. In parallel, we are looking at hydrogen-based ironmaking, for instance, and the synthesis of active materials for water splitting and subsequent analyses by APT to better understand how they form and what underpins their activity. So a relatively broad range of materials and problems.
What are the next steps for your research?
We’ve started making a dent into the possibility of analysing frozen liquids and liquid-metal interface, and that’s where the next frontier for us lies. The new facility at Imperial will help us perform these analyses at an unprecedented level of precision. We will be able to stop ongoing surface reactions, for instance, or wet corrosion “as it happens”, and these processes can be used to our advantage to tailor active surfaces, for example. This is extremely exciting for me!