Name: Jessica Tjandra
Position: PhD Student in the Department of Materials and Centre for Doctoral Training in Advanced Characterisation of Materials (CDT-ACM).
Research Group: Dr Stella Pedrazzini
Research Focus: The corrosion of additively manufactured titanium alloys for custom orthopaedic implants.
What inspired you to study for a PhD?
In the penultimate year of my undergraduate course (also in the Department of Materials at Imperial), I spent the summer as a UROP student working with Dr Stella Pedrazzini.
I was working on a Rolls-Royce project replicating salt corrosion in single-crystal nickel superalloys used in turbine blades in jet engines. On the first day of my UROP, Stella and I attended a Rolls-Royce meeting in Derby, allowing me to meet my industrial supervisors. What fascinated me the most was when Stella introduced me as her student who would be conducting the project – it was mind-blowing that in a room full of materials science experts, I could try to solve a problem that would affect all future Rolls-Royce engines! At the end of my UROP, we returned to Derby to report my findings, which was very fulfilling. There was a lot of scope for future research in the area, allowing me to continue my experiments as my final year project.
It excites me that I am trying to solve a problem that will benefit industry and society directly and see the concrete impact of my research in the future.
Can you tell us more about your research?
My current research focuses on the corrosion mechanisms of additively manufactured titanium alloys for custom orthopaedic implants. Implants such as knee and hip replacements tend to be made from titanium alloys that are forged (shaped into their final shape using applied forces, such as with a hammer or a die). Additive manufacturing (AM), or 3D printing, allows us to produce complex-shaped implants for patients requiring bespoke devices. This will hugely benefit patients who cannot utilise mass-produced implants, such as bone cancer patients, young children, and patients requiring revision surgeries from previously failed implants.
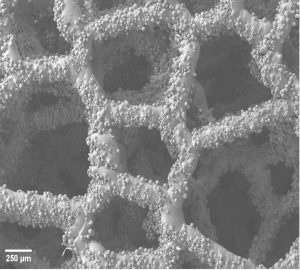
The issue with additive manufacturing is that the components produced tend to have defects from the manufacturing process. They also contain more oxygen which causes the component to be more brittle. The porous structure of the implants, called lattices, also means that they are more susceptible to corrosion damage. Once placed in the body, these implants will be exposed to blood plasma, body temperature, and forces from body movement.
My work replicates these environmental factors to AM titanium lattices to interpret the corrosion mechanisms of the implants, especially with applied mechanical loading. Knowing the durability and safety of AM implants is important as they will reduce the need for revision surgeries in the future, benefiting patients and the NHS.
I use materials characterisation techniques such as atom probe tomography (APT) and energy dispersive spectroscopy (scanning tunnelling electron microscope – STEM-EDS) to determine oxygen concentration around crack tips from fatigue loading and across grain boundaries with different crystal orientations. Furthermore, I work with colleagues from my industrial collaborator, Alloyed Ltd, to determine the best way to manufacture these lattices, with complex shapes and overhangs, accommodating components such as nails to attach them to neighbouring bone.
What does a typical day involve?
My day varies a lot depending on the stage of my PhD. Last year, I spent most days conducting many compression fatigue tests of my lattices, some of which lasted a month per test! Currently, I am mostly preparing APT samples using the focussed ion beam (FIB) facility. I usually spend a bit of my day reviewing new literature on similar topics, writing papers for publication, and making pretty figures that I can later use in conference presentations and my PhD thesis. The rest of my day usually involves meetings with my supervisor or undergraduate/master’s students.
Can you tell us more about your research group?
My research group (the metals electrochemistry group, led by Dr Stella Pedrazzini) is undoubtedly one of the reasons I enjoy doing my PhD so much. We meet once a week to update each other on what we have been up to, whether it is a failed experiment, writing research proposals, or going on holiday!
What do you enjoy outside of your PhD?
I enjoy doing STEM outreach and am an active Discover Materials Student Ambassador and Departmental Student Ambassador. Materials is such a great field to be in, and many people are unaware of its existence! I have delivered many workshops, lab demos and presentations to young people about my research and materials science at events like The Great Exhibition Road Festival, Big Bang Science Festival, Cheltenham Science Festival, College Open Days and more!
Outside of work, I enjoy cooking and baking. Coming from Indonesia, I also play the Javanese gamelan, a traditional ensemble music made up of metallophones, gongs and drums. We play at various gigs and practice every week.