Name: Connor Wright
Position: PhD Student in the Department of Materials
Research Group: Professor Mary Ryan
Research Focus: Connor is part of the newly founded InFUSE Prosperity Partnership, linking Imperial research with state-of-the-art techniques to progress the energy transition. His research focuses on the degradation of Sodium-ion batteries, widely considered the next big thing in battery energy storage.
What inspired you to study for a PhD?
Before university, I didn’t even know that ‘Materials Engineering’ was a thing. As anyone interested in the sciences at school does, I thought my options were limited to medicine, the natural sciences or the more classical engineering routes (civil, mechanical, electrical, etc.). It was only a couple of weeks before the UCAS deadline that I discovered – thanks to my sixth form tutor (thanks again, Mr Hunt!) – the wonders of Materials Engineering.
I applied for and got accepted onto the course at the University of Birmingham and have never looked back. The top-down approach, where you start with an application, assess the materials requirements, and then go to work on manipulating materials at the most fundamental level to achieve these, was something that really resonated with me. In my third year I chose a battery-related group project, thinking they were a worthy application to focus on with this top-down approach. In my Masters’ year, I again chose batteries for my individual project, focusing more on recycling. Continuing onto a PhD was the logical next step. I love the research culture, and where better to go than Imperial!
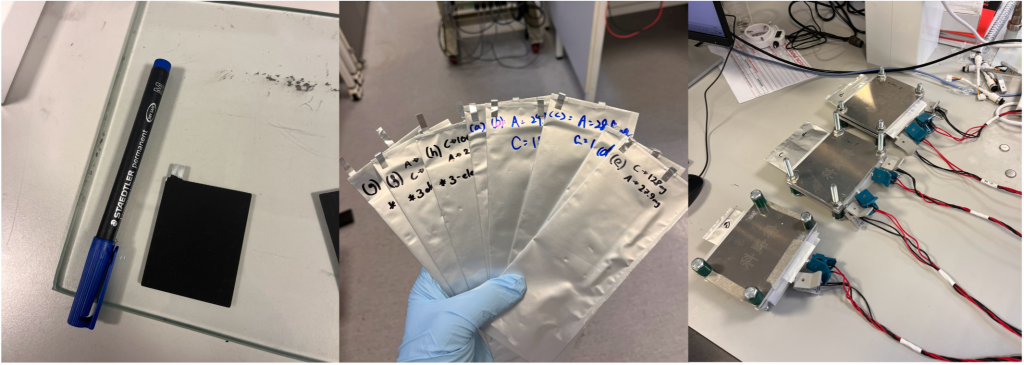
Can you tell us more about your research?
I focus on cathode materials for sodium-ion batteries (NIBs). Like lithium-ion batteries (LIBs) that we all have in our mobile phones, NIBs work by shuttling and storing positively charged ions and atoms, respectively, between two electrodes. The key difference is that NIBs use sodium, which is cheaper and more sustainable than lithium but heavier and less energy-dense. These properties make NIBs suitable for large-scale energy storage solutions and very suitable for renewable energy conversion like wind and solar. While current grid-scale storage relies heavily on pumped hydro, its cost and geographical constraints limit its global application. NIBs could be the bridge to a fully decarbonised society.
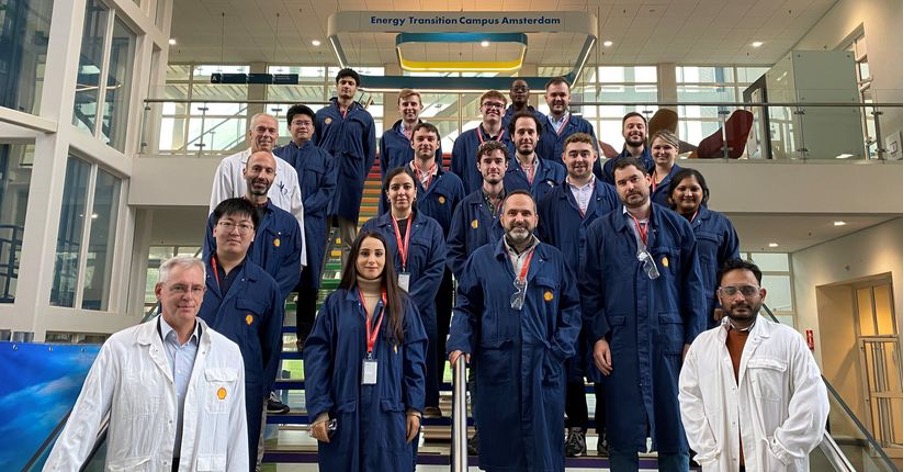
My work aims to understand why some promising NIB materials degrade as fast as they do. I engineer methods to study these materials at the smallest scale and in real-time, as they charge and discharge. These specific techniques are labelled ‘operando’.
At the UK’s national synchrotron facility, I conduct experiments that involve firing high-energy X-rays into my batteries to gather all sorts of useful (and awesome) information. One key technique, X-ray Absorption Spectroscopy (XAS), provides insights into the chemical and electronic structure of the host electrode material. Looking for unusual changes in the XAS signal as my target electrode charges/discharges is a large part of what I do as a researcher.
What does a typical day involve?
A typical day would see me in the lab making and testing batteries. Production is a complicated and multi-step process, so depending on which stage I’m at, this could mean using furnaces, slurry mixers, coating machines, or the testing/cycling rig. Most days will also involve some sort of data analysis, either cycling data from the lab or some more hardcore stuff from a recent synchrotron experiment. However, as with all research, no day is ever the same, and things are always changing!
Can you tell us more about your research group?
I work in two different groups, which is not uncommon here at Imperial. My primary supervisor is Prof. Mary Ryan in Materials, but most of my lab work is with Prof. Magda Titirici’s Battery team in Chemical Engineering. In my second year, I organised Mary’s biweekly group meetings and also went to both France and China with Magda’s group for conferences.
What do you enjoy outside of your PhD?
I wouldn’t be where I am today if it weren’t for sport. I’ve played field hockey my whole life, and throughout the PhD is no exception. I also love music and regularly attend a ‘pub choir’ in south London with many friends. Coming from a farm in rural Leicestershire, I also need my regular dose of fresh air and greenery, so I often take hikes out of London with my girlfriend.
Slightly closer to home, I enjoy my work as an Outreach Ambassador for the Department of Materials. As I said at the start, not many people know about Materials as a field, let alone a degree or career option, and that’s a real shame! I’ve done lab demos at Imperial’s Open Days, helped run stands at public events such as The Great Exhibition Road Festival and even organised my own event for 2023’s Pint of Science Festival.
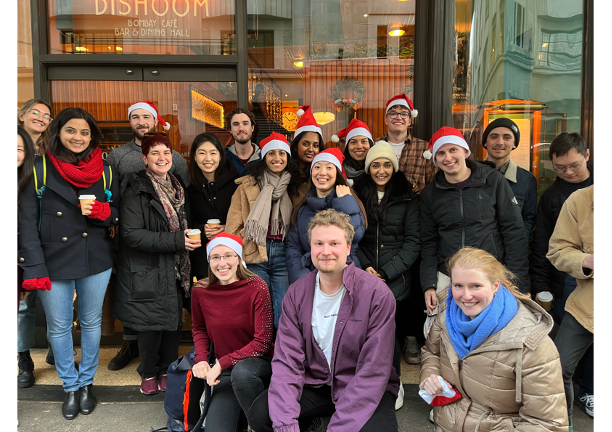